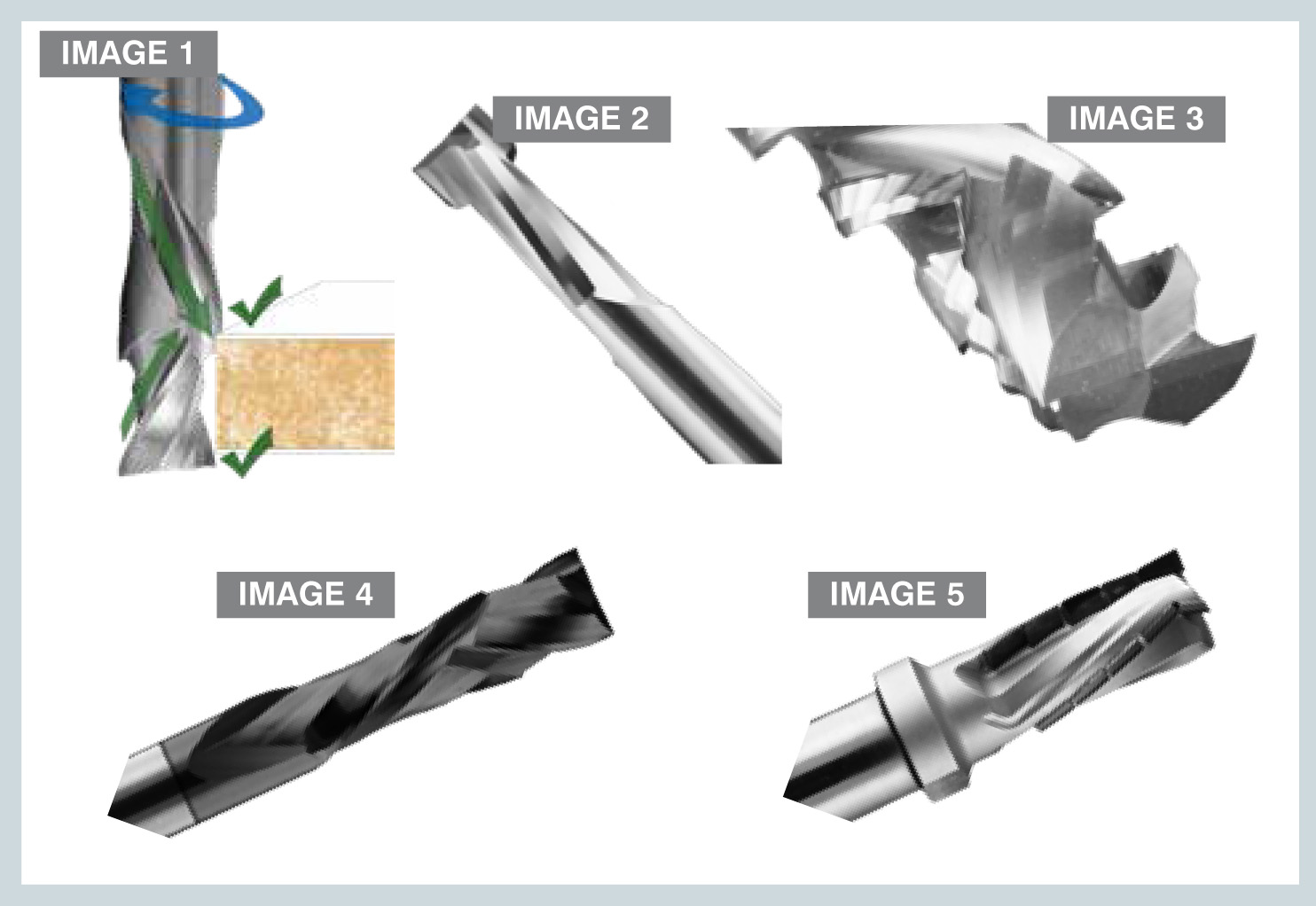
Compression router bits have become the most common router tools used in panel processing operations. North American growth in CNC router sales and a dramatic increase in panel processing requirements, has dramatically increased demand for compression spiral tools.
A variety of compression spiral designs have emerged to optimize machine performance on different material types and tool paths. A wide variety of options have made the tool selection process more complex.
Image 1 shows a traditional compression spiral design, which gets its name from the alternate compression shear indicated by the green arrows on image. This remains the most common design, but new tool geometries have emerged to improve processes and optimize cut quality on modern wood composite panel products. Traditional “straight flute” router bit designs could not successfully cut panel material without chipping top and bottom layers. The invention of compression spirals allowed machinery to operate at higher feed rates and improved cut quality on the top and bottom of material.
Compression spiral designs have evolved with altered geometry, to better suit specific materials and applications.
Image 2 shows low helix geometry which is designed to cut plywood and solid wood cores. Traditional compression tools with extreme shear, often create too much compression for certain wood products.
In this case, a lower helix
will reduce feathering on plywood and provide the best possible cut quality with minimal heat generation.
Image 3 shows a high feedrate compression with four flutes, and a chip breaker/finisher design. This geometry is intended for POD router systems and allows for highest possible feed rates without chipping. It will cut a range of materials, but is specifically designed
to reduce cutting forces on difficult melamine, high pressure laminate and other abrasive layers of panel products.
Image 4 shows a compression spiral with a coating to help dissipate heat, improve lubricity, and chip extraction. All the tool options shown above can be manufactured with coatings to improve tool longevity and performance. Abrasive materials generate excessive heat, which breaks down the cutting edge prematurely. Coatings can prevent heat generation, resulting in better cut quality and extended tool life.
Image 5 shows a polycrystalline diamond compression router solution. Traditionally it has been difficult to produce a diamond tool, which will perform equal to a carbide comparable tool.
However, diamond tools have proven to outlast carbide by 200 to 300 times, which is critical for extremely abrasive materials, which are emerging in the panel product industry. If carbide coatings will not hold an edge on these difficult materials, then diamond becomes the only option.
There are a variety of diamond compression choices available. The main difference between options is the number of flutes which effects chip load and feedrate limitation.
Single flute diamond tools have been available for many years. Due to minimal amounts of diamond material used, they are a cost-effective option. However, single flute diamond tools are limited to feed rates of 150 to 300 inches per minute. Double flute diamond compressions can generally run up to 700 inches per minute, depending on the density of material. Three flute diamond compressions have proven to run above 800 inches per minute on standard medium density particle board. However higher density boards and more abrasive top bottom layers will require a feedrate reduction.
Three-flute
compression optionsNone of the images show three-flute compression spirals, which are available from a variety of tooling manufacturers. However, three-flute tools have not proven to outperform two-flute designs in most scenarios. Nested router applications do require sufficient space for chips to be extracted. Three-flute tools do not always provide enough flute depth or chip flow for optimal chip extraction. Two-flute designs are generally better suited to nested router applications at standard feed rates.
There are some scenarios where smaller chip loads are needed, a three-flute tool can be used. However, it is critical that RPM and feed rate are considered to avoid excessive heat generation. A three-flute compression tool must be run at high feed rate, and spindle speed should be reduced to 16000 RPM to prevent premature cutting-edge failure.
Length of up-shear considerationsUp-shear is defined by the length of cutting-edge shearing upward from the spoil board or bottom of the part. This dimension is of importance, because it has a dramatic effect on upward chip flow into dust collection systems. Minimal up-shear will prevent chips from being extracted effectively from the cutting area, resulting in excessive heat generation
Longer up-shear can cause the top layer of the panel product to chip, due to upward pressure. This can also occur during the plunging operation, so careful attention to ramp angle while plunging is important. To determine optimal up-shear, it is important to consider the thickness of material, and operations being performed with the tool.
For example, shallow dado operations will require a short up-shear to avoid blowout on the top layer of panel. However, short up-shear compression spirals are not as efficient when cutting at full depth on 3/4 thick panels. Other solutions exist by using separate tools to perform shallow dado applications and through-cut operations.
Average up-shear dimensions of 1/2-inch diameter compression tools ranges from 0.200 to 0.625, so consider the variables of your material and toolpath operations before selecting the proper tool. A basic rule is to use the longest possible up-shear to improve chip flow, but not too long to sacrifice cut quality.
1/2 inch VS 3/8 inch diameterMost compression tools used
in the industry are 3/8 or
1/2 inch diameter, as they are best suited to nested router manufacturing. There are several considerations when deciding on the optimal diameter for your operation.
Material yield is a factor, depending on the cost of material being machined. In some cases, 3/8 diameter can allow for additional parts to be nested, but this is normally not an issue for standard priced panel products.
Tool stability is a factor at higher feed rates, to avoid tool deflection or breakage. Half-inch diameter tools do remove higher amounts of material, resulting in additional cutting pressures. However, ½ inch diameter carbide rods are generally less likely to break, and less prone to deflection in the collet.
Sharpening requirements are an important factor which will affect performance and cost analysis. Half-inch diameter compressions can be sharpened two to three times, assuming machine operators are willing to use diameter compensation in software.
By comparison, 3/8-diameter compression tools can only be sharpened realistically one time, before geometry changes have a negative effect on tool life and cut quality. The decision is really based on access to quality sharpening, and the willingness to use diameter compensation. Some manufacturers find the risk of diameter variations too high to justify sharpening tools and dispose of tools after single use. Other companies who have access to precision sharpening and have operators willing to use software features, find good value in sharpening.
Initial tooling cost is obviously lower for 3/8 compressions, which may be attractive for companies who choose not to sharpen. But the initial cost of the tool must be balanced with all the other performance considerations.
ConclusionCompression router tooling solutions have been a critical factor in CNC router efficiency and performance improvements. Premium cut quality at high feedrates would not be possible without tooling innovation and design of new compression router formats. As material composition and machinery demands have continued to evolve, a greater selection of compression routers has become available.
Take time to consider the proper compression router design for your material
and application.