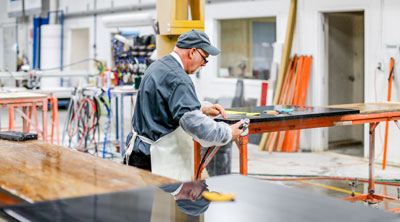
We all know we need to improve our operation.
We need to do this on top of the hundred other things on our plate. The other things are daily production and emergencies of all kinds. So, if you are not consciously pushing to get started on improvement projects, they are falling by the wayside, waiting for a time when you are not so busy. By now we have learned that these ‘not so busy times’ never really come.
If you want
something done,
ask a busy person!I like this proverb.
Even when you are busy, you can always take on an extra task. When you are already busy you need to be creative on how to prioritise and squeeze these other tasks in, or even delegate some tasks.
So, the first step is taken.
You have time!
Step 2: What are the objectives? What are the most pressing issues short-term, mid-term and long-term? For example, is product quality the daily challenge; is it your on-time shipping; do you have enough capacity or not enough work? Pick the one which challenges you and your team the most. It helps to write them down. Eliminating these challenges is now the written objective.
Do you have the facts, or just an opinion?Numbers are important! Can you back up your performance with repeatable measurements? Especially in my work, I like to establish measurable performance indicators (KPI). So, if I find on-time performance is the challenge, I will immediately try to have a simple measure in place. If it is the cost of quality which is a challenge, I will develop a measurement to monitor that.
How else would we know if we are getting better? Or, how will we find out if corrective actions put in place are having any impact?
Change comes slowly and incremental improvements are not “felt” right away. However, if good KPI’s are in place changes and early trends become visible.
Step 3: Get started
Immediately put actions in place to support the objectives. To wait until all ducks are in a row will cause you to miss opportunities. Learn from the early steps and improve your methodologies.
Step 4: Get the employees involved and engaged
If it is your project and you are doing it, you need a lot of time and energy to sustain the change. By getting more people involved and convincing them of the importance of the change, there is a higher chance of sustainability. Communicate with the people on the objectives and the results.
Step 5: Go back to Step 2
and repeatThat is all that Continuous Improvement is about. I want to dive a bit deeper into some of the elements, but the important point is that you drive for a change in the culture. We need to improve and get better. Everybody can and should/must participate. What is important is to co-ordinate the effort and the direction in which the team is pulling, and also to find the balance between directing the team and allowing for their own creativity to flow.
We all know the story: Give a man a fish, and he will have food for a day… In our companies when we teach our employees lean manufacturing, we are doing the equivalent of …teaching the man to fish.
Initiating the culture change is the most important element. The fact that the employees know 5S and know how to create a shadow board, or how to set up a KANBAN driven inventory control is fine, the real positive impact comes when the employees start to think in lean manufacturing terms and understand and recognize waste.
Pull!Manufacturing plants sometimes find their equilibrium, they seem to be working just fine at a certain level. Teams often do not want to touch this type of a situation/system since it is working. They don’t want to fix what is not broken!
So, if you want to increase the throughput volume or reduce the factory throughput time, you run into some resistance. To discover what needs to change, you put more “pull” in the flow. You
pick a location in the process chain, down-stream from a possible/expected bottleneck and increase the capacity a notch. Basically, it is similar
to comparing a process or operation with a driven conveyor: Make the wheels at the end of the conveyor turn a little faster. It does not produce more output, because you are not feeding more onto the conveyor. But as you speed up at the end you are pulling slack out of the system.
In real production this means that we are reducing material buffers where they are not needed. This “pulling away” works until you reach a bottleneck. A true bottleneck can only produce its capacity and not more. Often just clearly identifying this bottleneck helps to find solutions. As a bottleneck gets some relief, another process step will limit the overall throughput. Again, if you pull downstream, the limitation will show up. These bottlenecks would not be as visible if you would push more orders into the factory. It would just mean that there are more carts with material and orders on the shop floor. Employees will ask for more space and a bigger factory. The more you push material on the shop floor the longer your factory throughput time becomes. Your productivity will actually go down.
Identifying and finding the bottleneck or the constraints is a practical method to set priorities. If you improve something that is not a constraint, the overall improvement is often minimal. However, if you improve a bottleneck/constraint process,
it will increase the productivity of the entire operation.
Getting the improvement process started is the most important part.
Inaction is the constraint.
As you get started you will learn to prioritize the most pressing issues and solve them first.