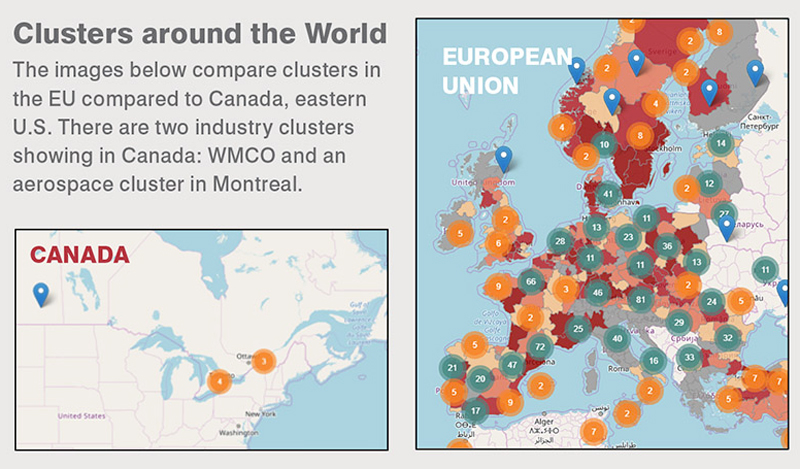
In our last column we introduced the Wood Manufacturing Cluster of Ontario (WMCO). We offered some background and context on the evolution of the cluster and how it got to where we are today. Representing all segments of the value-added wood manufacturing industry, we are industry-led by a very engaged volunteer board of directors consisting of 10 manufacturing members, and three supplier associate members. In June this year, our board completed a five-year strategic plan. I will explain more about that later in the article.
But first, what is it about this word “cluster”? What does it really mean?
It may be a new word to many readers, and for some of you it may be a word you have heard spoken by other industry leaders, politicians, or government economic development representatives. It has become a trendy word found in government programs, and is loosely used to describe a group of companies or industries in a region.
But there is a true definition and discipline behind industry clustering that was theorized by economist and business strategist Prof. Michael Porter of Harvard University back in the early 1990s. His cluster theory has been embraced and is being used to guide local and regional economic development policy and strategy by most countries in the EU, by the Organization for Economic Co-operation and Development (OECD) and other countries around the world (Google Michael Porter and clusters and you will see hundreds of articles and news feeds).
So, clustering has been around for 30 years and the EU countries are 30 years ahead of us. But what is clustering really in the practical sense, and how are clusters different from associations?
Simply put, Porterian clusters focus on one industry, one region, the manufacturing companies, the supply chain, academic partners, other industry partners and government stakeholders. The idea is that when you combine all of these stakeholders; and facilitate collaboration between competitors and the supply chain, channel feedback to post secondary institutions for workforce development, involve government for support of collaborative projects, and facilitate collaborative activities that provide impact and value to the companies, the industry at large becomes more globally competitive vs. expending energy competing within itself. The last important differentiator is the cluster becomes a non-profit corporation; led by the manufacturers with board governance.
Clusters take 10-15 years to mature, with government assistance to get them started, and gradually building revenue streams to be sustainable; but a small amount of support from government partners always remains to support collaborative project activity.
Some examples of how the WMCO cluster adheres to the cluster model can be found in our programming (training), events (plant tours, Kaizen, networking, member driven topics) and collaborative projects (export readiness, international trade shows, and digital adoption/Industry 4.0). These collaborative projects, programs and events get competitors talking to each other and finding common ground: a central focus of the strength of clustering and global competitiveness.
For the academic partnerships, the focus is workforce development. WMCO has a seat on the program advisory committees (PACs) for three post secondary woodworking programs: Conestoga, Humber, and is chair of the PAC for Georgian College. The role on these committees is to make sure the voice of the manufacturer is heard when it comes to course curriculum and program development. This is so that the colleges are teaching the right things, and graduates from these programs have the right skill sets to enter the workforce in your shops. Members attend these meetings with us and give advise to the teachers. At the Georgian PAC, we review courses at every meeting, so this feedback is in real time. WMCO also sponsors 25 high schools in Ontario for the Wood Manufacturing Council’s WoodLinks program: a curriculum for high school shops; since many young people enter our workforce right after high school.
The role of academia in EU clusters is also to conduct research to quantify the impact of clustering, by studying and monitoring impact on the companies KPIs, thereby justifying support of the clusters. We are currently working toward getting this level of engagement with academia here in Canada.
As mentioned, EU countries have made clustering central to their local, regional, and national economic development polices and strategy. For many EU regions, you need to be a member of an industry cluster to even get a business license. That’s how entrenched it is in their industry culture, and with government, with funding models to support industry. The results for countries like Germany (Industry 4.0 adoption - which is 10 years old now) and Italy speak for themselves. They are benchmark countries for our industry for technology, automation equipment and design respectively. For those of you reading this article and who have friends, acquaintances, business partners or customers with manufacturing operations in the EU, ask them about industry clusters in their regions. The answer will likely be a long one explaining what clustering activity is taking place.
So what makes clusters different from associations? One answer can be found in geographic coverage. Clusters are very regional in focus whereas some associations have national mandates. Another difference is the focus on collaboration, leveraging government funded projects, and events, designed to get competitors talking to each other and sharing best practices and challenges. The academic link described earlier is another example. In Austria for example, they have seven different clusters making up one large national cluster.
Where a cluster may not exist, enhanced virtual engagement now allows companies to participate in clustering activity outside their region with other clusters, as is the case now with WMCO, with member interest coming from not only all parts of Ontario, but from across the country as well.
The engagement of supply chain is another difference: while supplier members are embraced for their expertise and knowledge to support the industry, they do not have all of the same privileges as the manufacturers. For example, they have to be invited to the plant tours by the host in order to attend so the right suppliers are chosen for the Kaizen exercise to provide value. Another example is with the WMCO cluster board governance; suppliers cannot become chair, and while suppliers can vote, they cannot contribute to a quorum. Also, the WMCO cluster does not accept large sponsorships from suppliers, creating a level playing field for all and keeping the organization manufacturing centric.
Why is clustering so new here in North America and not as common?
The answer to this question lies in the need for trust and foresight in our business culture in North America to be open to collaboration for the greater good. For many this is a new concept and WMCO is leading the charge in Canada as the only true cluster in existence for the value-added wood-manufacturing industry. It also goes back to the lack of understanding on the part of our governments to support the core activities of clusters. Clusters are a long play, taking up to 15 years to truly mature. It takes political will and commitment across government mandates to establish clusters. The proof of their success is evident around the world.
As mentioned earlier, the WMCO cluster board of directors has just completed a five-year strategic plan with a new vision, mission, guiding principles, and strategic directions:
WMCO Cluster Vision: WMCO’s leadership is strengthening the performance, innovation and agility of Ontario’s value-added wood manufacturing industry.
WMCO Cluster Mission: WMCO’s cluster model generates collaborative relationships to share knowledge, stimulate innovation, and foster new mindsets and ways of working together.
WMCO Guiding PrinciplesWe will do our best work together when we:
Collaborate with each other;
Share best practices and emerging new ideas/technologies;
Create an engaged community;
Respect diverse viewpoints;
Seek synergies between our companies and partners (government and academia);
Value the support and innovation of our supplier members; and
Conduct our business in a fair and ethical manner.
WMCO Strategic DirectionsInvest in Building Strong Relationships
Attraction of members/partners
Retention of members/partners
Outreach to Strategic Partners (Regional, National and International) to support sustainability, programming, and new initiatives
Design and Provide High Quality Programming
Events
Training programs
Collaborative Projects
Enhance our Sustainability
Internal Revenue Development – membership and programs
External Revenue Development – government funding, special projects, and emerging opportunities
You can learn more about the WMCO cluster at
www.wmco.ca