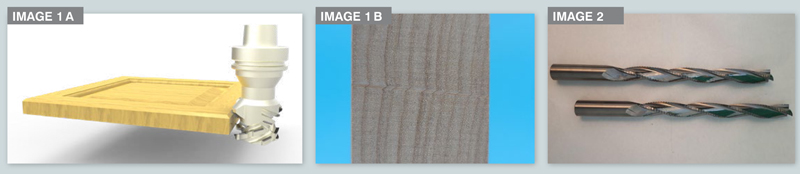
It was refreshing to be back in the tradeshow halls at IWF in Atlanta to collaborate with customers and suppliers to address the needs of a changing production environment. Machinery, software, and tooling innovations continue to evolve and fuel a driving force to automate the woodworking industry. A severe lack of reliable labour is forcing automation of machining and finishing processes like never before. Although cutting tools are only a part of the automation equation, they do have a dramatic impact on automation efficiency and the final quality of products. Obviously, automated sanding and spraying machinery do not involve cutting operations, but cutting accuracy and quality on other machines before sanding and spraying equipment must be considered in the efficiency of the entire production line. A variety of tooling trends were highlighted at IWF from all tool manufacturers helping to support the automation process.
High shear innovations to improve efficiency and qualityHigh shear diamond tooling is transforming machining capabilities at high feed rates and generating cut quality improvements never seen before in the woodworking industry. As machinery designers have pushed to increase feed rates over the years, cutting tools have been a major limiting factor as premium cut quality has been difficult to achieve on a consistent basis given all the variables in material composition. Metal markets have been more successful as steel is relatively consistent to machine compared to the many variations of wood species, moisture content and grain structure. However, high shear tool geometry has proven to be an equalizer in the quest for premium cut quality at high feed rates.
Image 1A shows an example of a high-shear cutting tool machining a door edge. These tools were featured by various tool manufacturers at IWF in router bit and cutter head format.
Image 1B shows a magnified illustration of a cabinet door cut with high shear geometry. Notice the premium surface finish and lack of grain tear out which is problematic with traditional tooling. This type of cut quality has been made possible only with high shear geometry and has been proven to dramatically reduce finishing time and resource requirements.
Material cost reduction As material costs continue to fluctuate, it is imperative to find ways to reduce or eliminate part defects, which substantially increase raw material costs. Large parts such as entry doors and tabletop components generally require final perimeter cutting operations, which are often difficult with traditional tooling geometry. Due to size and complexity of parts, there is always a substantial raw material and production time investment prior to the final sizing operation. If the cutting tool tears out grain or provides unacceptable cut quality, there are inevitably additional finishing requirements or in some cases the entire part must be replaced. High shear cutting geometry dramatically reduces the chance of defects in the final perimeter cut operations, resulting in material cost reduction of high value parts.
Decrease machine
cycle times High shear geometry has proven to provide premium cut quality even when machining at high feed rates. Many customers have reported a 25 to 40 per cent increase in allowable feed rate using high shear tooling without any sacrifice in cut quality. In specific wood species, that number can be even higher as certain wood species such as Alder and Douglas fir must be run extremely slow when using traditional geometry cutting tools. High Shear cutting edges seem to cut all wood species with very little difference in cut quality between species. This allows the machine operator to use the same tool for all types of wood to avoid tool changes, resulting in greater machine efficiency and less labor to change tools.
CoatingsOften, smaller diameter tools for CNC routers cannot be manufactured in high shear diamond or other geometry due to design limitations. In this scenario, various coatings can be applied to solid carbide tools to improve tool performance and longevity. Tool manufacturers at IWF featured a wide variety of tool coatings in various colours and compositions. Regardless of coating name or colour, they provide similar benefits and performance when routing abrasive materials, which generate excessive heat, resulting in premature cutting-edge failure. Coatings help dissipate heat by increasing the hardness of cutting edges and adding lubricity to the flute of router tools, reducing heat generation and cutting-edge failure. As the industry has transitioned from solid wood-to-wood composites and hybrid materials, coatings have proven to be a valuable partner in the quest to extend tool longevity and reduce the requirement for tool changes.
Extended length In our industry, traditional length of tooling has ranged from two inches to eight inches in overall length, which generally allows for ½-inch to six-inch depth of cut. Limitations in carbide raw material and grinding equipment capabilities made it very costly, or in some cases impossible to produce extended length tooling. However, router-tooling exhibitors at IWF showcased many large format routing tools used on various CNC equipment. Advances in grinding equipment and greater supply of long length carbide raw materials have allowed tool designers to push the limits of tool extension. Tool holding innovations have also been a valuable support for large tool performance in extended reach applications.
Image 2 shows a 12-inch-long tool designed to machine CLT material on a CNC router and perform operations previously impossible without extended length tooling.
These types of tools must be treated with extreme care when handling and setting up on CNC machines to avoid costly damage. CNC programmers must use good judgement to adapt machine parameters and use proper tooling holding methods to ensure safe operation.
If extended length router tooling is used properly, it can drastically increase machine flexibility and
perform operations not normally
possible on CNC machines.
Aggregates to improve machine flexibility
In recent years, five-axis machinery has been more commonly purchased in favour of aggregated technology for various reasons. Most importantly, the cost of 5-axis technology has decreased to make aggregate technology less attractive to purchase. However, given the current delivery challenges facing all types of machinery, it is very difficult to integrate equipment quickly. Therefore, manufacturers must find ways to optimize the performance of existing machinery and aggregates provide a quick option to improve flexibility of 3-axis machinery. A wide variety of aggregate designs can replace operations, which were previously performed manually off the CNC machine. Aggregate versatility has also improved with new “quick connect” innovations
which allow for fast changes
from saw blades to router bits to cutter heads in only seconds. All these small advancements in technology can compound to optimize machine output and reduce labor requirements.