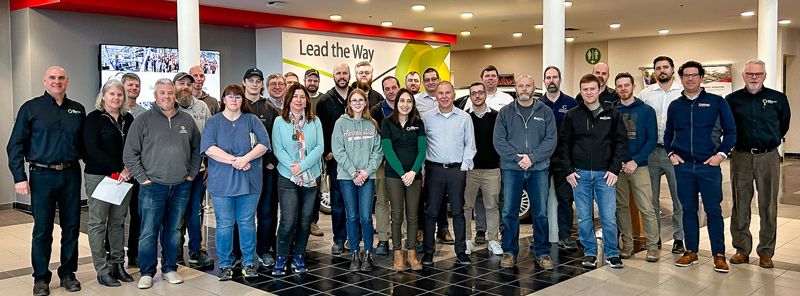
Photo: Contributed
Members participate in the WMCO Feb 22, 2023 Toyota Plant Tour and Lean Debriefdiscussions hosted by Royce//Ayr.In my last column, we examined how industry clusters harness the synergies of competition to raise the capabilities of an industry’s performance, to become globally competitive. The fact that this applies to both suppliers and manufacturers, amplifies the value of cluster networks whereby the individual manufacturer can leverage the knowledge, skills, and abilities of those around them to improve and thrive.
While initially counter-intuitive to traditional competitive mindsets, more than 400 industry clusters exist in the EU alone. Canada’s main competitors in our industry, such as Sweden, Finland, and some eastern EU countries, have been leveraging clusters for more than 30 years. Sweden and Finland alone each have three established wood industry clusters. Those clusters inform the government on policy to assist their industries and execute government programs for their members. One additional unique feature of industry clusters is they recognize the need for benchmarking and learning from other industries outside their own.
The Wood Manufacturing Cluster of Ontario (WMCO) has been actively engaging the Toyota Production System (TPS) as one of our themes for programming and change for our industry. Our members have used it as a model for continuous improvement and eliminating waste for the past 11 years. The TPS system was initially responsible for the success of Toyota in the 70s to emerge as a leader in the automotive industry ahead of the likes of GM, Ford, and Chrysler. The discipline, which is based on creating a culture of empowering their employees while following a systematic disciplined approach, has been adopted across industries far beyond the auto sector. The TPS, also known as Lean manufacturing principles, has been applied to health care, education, and Canada Post. Most recently, WMCO has begun a path for wood manufacturing companies to apply the principles to the office and administration functions (Lean for the Office).
But really, how can an automotive manufacturing system be relevant to wood manufacturers? Why do we need to benchmark our activities with other industries?
First of all, the five principles of the TPS (Lean) apply to any business process, along with their seven deadly wastes.
When you look at them and think, you realize that they do.
Here they are capsulated in a convenient table, and a few examples of various lean tools.
Manufacturers in the wood industry are on a constant journey of continuous improvement to reduce and eliminate waste in all its forms, to become more productive and sustainable for the future. Benchmarking our wood product processing to TPS lean principles and tools is an important activity to undertake to take our businesses, and our industry, to the next level of economic output and performance.
To that end, on Feb. 22, WMCO hosted a tour for members at the Toyota Cambridge Plant. Our tour began at the Experience Center where our visitors were able to interact with the interactive displays in the showroom. Members were primed on what to look for in reference to lean activities, and for ideas and concepts that can apply to their operations.
Following that, we watched a welcome video before embarking on a motorized tram tour of the Cambridge Plant to learn about how team members and robots build the Lexus RX350 and 450h. While WMCO members rode a motorized tram into the activity, trained tour guides spoke directly to us via an audio headset.
The flow of the operations was explained and the various processes were highlighted. Interesting aspects to consider is how they manage custom mass production, with the flow of diverse parts and colours that all convene at one place at the end for final assembly phases. The work of teams was evident everywhere, as well as clear visual plant communications, to help inform employees and management how they are performing in real time. 5S was also evident everywhere.
Once the tour ended, WMCO members reconvened at Royce//Ayr Cutting Tools in Cambridge, for a hosted lunch and further Lean debrief discussions with the help of Julia Novik, president of Lean Advisors. She provided a review of Lean principles and described how the tour related to improvement activities in wood manufacturing operations.
Thank you to Grass, LMI Canada and Upper Canada Forest Products and Royce//Ayr for sponsoring and hosting the lunch.
After networking and further Q&A, the event was a success, and everyone was able to leave with insight on how to apply what they saw to their own manufacturing operations. The learning journey continues and never ends, which is why WMCO hosts tours like this one at Toyota every year.
External benchmarking is extremely important for our industry if we are to become globally competitive and thrive in an ever-changing market place. The ecosystem of manufacturers who are on the same journey allows you to compare and benchmark with your peers; this is part of the value of cluster networks.
The WMCO is working on more benchmarking opportunities for our industry, to help us understand how we are doing, and what we need to improve to do better. Stay tuned!
Get involved now with the only cluster for the wood industry in Canada. You can learn more here:
www.wmco.ca, or contact us at
mbaker@wmco.ca