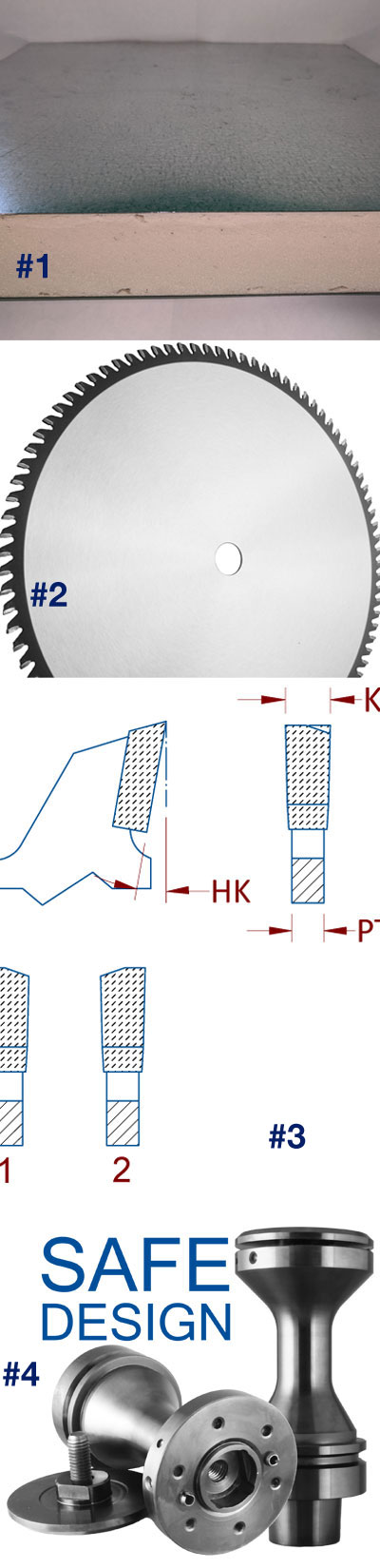
It is not recommended to cut all types of metal material on a CNC routers designed for wood machining. However, it is possible to cut thin gauge steel under optimal cutting conditions. Softer metal products such as aluminum, can be machined effectively on CNC routers using specialized tooling and machine parameters, but steel products do present a challenge, which can only be overcome with specialized tooling and machining processes.
Most steel products are cut using a cold saw at low RPM, using flood coolant, or laser and plasma technology. Thin gauge steel skin can be cut with a saw blade on a CNC router under very specific conditions. Regardless of cutting tool and material, there is a chance of sparks causing ignition on the machine or in the dust collection, which does present a very serious safety risk. However, a properly designed machine with adequate hold down pressure, safety guarding and cooling units can create an environment to cut thin gauge metal skins effectively.
In recent years stainless steel skins have become common in countertop applications and other commercial products. Despite many challenges it has become possible to cut these materials on CNC routers using specialized router tooling. But in some situations, there is a requirement to use a saw blade due to thickness of material.
Image 1 shows an example of a hybrid sandwich material with high density foam between metal skins. This type of material has been in used in entry door and garage door industries for years. However, a wider range of products is expanding rapidly as innovative product designs evolve in residential and commercial building markets. Most products can be cut effectively with traditional saw equipment with specialized saw blades, but a need for labour reduction and has increased demand for use of saw blades on CNC router designs. Saw blade design and tooth geometry is a critical factor to ensure safe operation and cutting success.
Saw blade design and maintenanceIt is very important to understand that any attempt to cut steel material with a carbide tip saw blade wheel result in minimized tool life compared to cutting other materials. Most other steel materials are cut with specialized cold saw machinery and saw blades, which does produce the best tool longevity. It is impossible to duplicate this type of cutting performance on a CNC router. However, it is possible to cut specific materials with success, if everyone is realistic about the restrictions and limitations of the blades. Use of flood coolant is not possible in many situations, as hybrid materials cannot be contaminated with oils or water. Therefore, specialized carbide tipped blades have been designed to install on CNC routers.
Image 2 & 3 show a saw blade with special tooth geometry required to cut thin gauge metal effectively. This tool style will provide the best combination of cut quality and durability, using a softer grade of carbide to improve impact resistance.
Saw blade holding systemsWhen saw cutting metal skin products on a CNC router, it is extremely important the saw blade holding system is rigid enough to support the saw and any potential vibration. Some CNC routers are custom built with a fixed flange system for saw blades. However, it is possible to use an HSK saw blade holder on a standard spindle of a five-axis CNC machine.
Image 4 illustrates an HSK integrated saw blade holder designed to maximize performance and safety on CNC routers. The integrated holder design will prevent excessive vibration and support the saw body with a safety cap on the outside of blade. It is not recommended to use a shank style saw blade holder or counter sink holes to fix the blade to the arbor. Metal cutting applications are more demanding than wood cutting, so saw blade holding pressure and accuracy is critical.
Vibration
Effective hold-down pressure on parts, is one of the most important factors to reduce vibration.
Properly designed saw blades will cut these materials effectively if the parts are held securely. Pneumatic clamping systems or manual clamping strategies can be used on the router bed to hold parts securely in place.
CoolantHeat reduction is the greatest challenge for any steel cutting application and coolant is an important factor. Traditional steel cutting saws use flood coolant to moderate saw blade and part temperatures. Since flood coolant is not an option for various reasons, misting stations are required to distribute a lower volume of coolant directly onto the cutting area to mitigate heat generation.
If materials are sensitive to cooling products, there must be some product assessment to avoid contamination while using some type of cooling solution. Steel cutting should NOT be attempted without some level of misting or cooling strategy.
Machine parametersThere is a variety of online information dedicated to routing applications for thin gauge steel. But very little exists to support saw blade applications on CNC routers. Given material variations, it is impossible to identify exact machine parameters, but there are some basic principles to follow.
RPM is a very important factor which must be considered. Saw blades under 14 inches generally run between 3000 and 5000 RPM. When cutting steel, the spindle RPM must be reduced to the lower end of the range, to control heat and limit saw tip fracturing. Feed rates will range based on material thickness and material clamping forces, but the goal should be higher feed rates if possible. Slower feed rates will improve cut quality but can overheat the saw blade quickly.
CNC routers provide many opportunities to improve operational flexibility and allow for flexibility in machine parameters, which is very helpful. Some saw equipment has fixed RPM and feed rate, which is not ideal for steel cutting. CNC routers do have the benefit of easily adjustable RPM, which can be reduced if heat generation becomes excessive, or change feed rates to alter chip loads.
ConclusionAs new material designs evolve, cutting solutions also need to progress.
Hybrid materials with metal skins, do present many cutting challenges when using a saw blade on a CNC router. Careful consideration must be made before attempting to cut these materials. Additional safety measures need to be implemented with adequate fire suppression and cooling components. With properly designed machinery, tool holders and saw blades, it is possible to cut new steel skin products effectively on a CNC router.