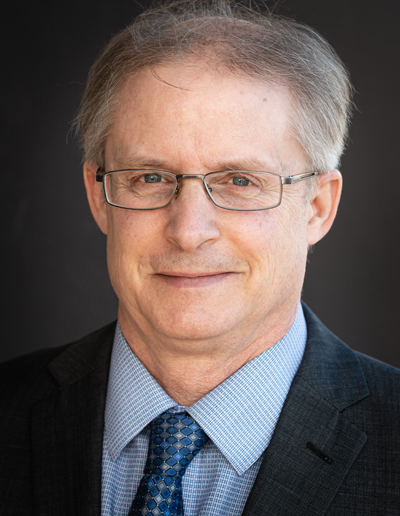
Photos: Contributed
Richard Lipman
Programs & resources for industry professionalsJust like everybody else, the Wood Manufacturing Council - a non-profit corporation that works to bring together stakeholders in advanced wood processing industry – has had to make adjustments because of COVID-19.
Between 2019 and 2020 they’ve trained 106 people, but there were fewer new opportunities in 2020. The overall success rate is 73% over that period.
“It has been challenging because we too had to make changes to the way we do things and that has led to some delays and postponements of some of our programming,” says WMC President Richard Lipman.
“Norma Picker, who manages our pre-employment training program nationally, works out of her home normally anyway and we kept the office open, as I am the only person who works out of there. And since other tenants also worked from home wherever possible, the building was mostly empty, so I came to work here, as I was more isolated here than anywhere else.”
Lipman said they had one course running at the time, and it shut down as they closed the training facility, but they restarted it as soon as they were allowed - with new social distancing, masks and all other COVID-19 requirements.
Lipman said the work experiences were impacted as well, but everyone adjusted.
Since some of their courses are delivered right in shops that have agreed to work closely with the Wood Manufacturing Council, those shops had to be re-jigged to comply with the new mandates.
“And we did get an indication that things were improving when we started getting approvals (and the go ahead to start recruiting)
for additional training courses in New Brunswick in the summer,” he said.”
WMC’s mandate is to “plan,
develop and implement human
resources strategies that support the long-term growth and competitiveness of Canada’s advanced wood products manufacturing industry
and meet the developmental needs of its workforce.”
Canada’s advanced wood products processing sector is large and growing and makes a significant contribution to the Canadian economy through the numerous businesses and enterprises, which make up the sector.
Advanced wood processing is comprised of five sub-sectors – furniture, cabinets, windows and doors, millwork, and factory-built housing and building components. Within these sub-sectors there are more than 9,200 companies.
The total value of the sector’s manufacturing shipments was estimated at around $17 billion in 2003. The value of its exports at that time was around $8 billion.
Clearly, the industry represents an important part of Canada’s economy, but it also faces substantial challenges. According to WMC, Canadian wood products manufacturers are experiencing an acute shortage of employable people. This is a common and urgent concern among firms of all sizes, and within all sub-sectors.
A WMC-commissioned study – the Wood Manufacturing Council Human Resource Sector Study – has identified a range of employment and labour market issues related to the apparent shortage of labour including an acute shortage of vital skills. Based on extensive interviews with advanced wood products manufacturers and related parties carried out as part of this study, the study concludes that the ‘skills gap’ is due to a wide range of direct, indirect and frequently interlinked factors.
Pre-employment training“In order to address some of these findings we have focused a lot on pre-employment training and included in that would be the idea to try and reach out to some under represented groups, so we have done courses for newcomers, women in trades, indigenous groups and so on,” Lipman says.
“Ultimately we are still doing some career awareness for the industry to take some of that initial recruiting pressure off the manufacturers in those regions where we are operating these programs and to get people some safety and basic skills for employment readiness before they get hired.”
Lipman says primarily what they are doing is going into areas and find governments that are interested in skills development to help people find work. And once they have a location they approach employment agencies or immigrant-serving groups or indigenous bands.
“So we are going to people who have clients who they are trying to find employment for and then we work with them in order to identify prospects.”
COVID-19Of course COVID-19 has impacted that work as people and governments are taking more time to make decisions because of the uncertainties, and yet at the same time there are certain areas and regions where they want to get going and we have been able to start some new initiatives.
“As I said, some of the projects were shut down temporarily as everyone was coming to grips with this unprecedented situation, but they are all back up and running now,” he says.
“So there were some closures and delays when communities locked down and kept people from outside the community out, which also means we couldn’t go in and we lost a number of weeks, but we commenced programming once we were allowed to open again.
“Right now we are doing an indigenous project in Southern Alberta and that shut down for a bit because of COVID-19 and then it reopened and started again.
“Of course that involved changing procedures and processes to make sure that we were sanitary and socially distant and all those sorts of things.
“And then another area is in The Maritimes, in New Brunswick, where we are seeing interest for our project.”
And while many learning institutions have switched to remote learning, Lipman says they frequently work with clients who don’t have access to the necessary technology for remote learning and working and that can be challenging.
“However, in most cases we do the training in a wood shop and we have been able to adjust the spaces and layouts where required in order to comply with social distancing requirements.”
Lipman says they go on site occasionally and certainly help with the initial set-up and preparations, but for the most part they are project managers, which mean they hire the expertise needed locally to deliver the program.
“When we are in a position where we can, our first choice is always to use the post-secondary education facility that has either a furniture or cabinetmaking program. We’ve used Algonquin and we’ve used Conestoga for example. And when we were in Toronto and Humber College was fully booked, we used the construction and carpentry lab at George Brown College. We’ve also used the Manitoba Institute of Trades and Technology and New Brunswick Community College and we do that because we want to make sure we have the best possible facilities and the best-possible instructors for our participants,” he says.
And then in terms of instructors, when they are doing contract training with the colleges, the college in question also usually provides the instructor.
“And our experience with doing it that way has been really, really good,” Lipman says.
“And otherwise, if there is not a community college available, we’ve used indigenous training centres, we’ve used high schools and private career colleges, a little bit of everything really, but we are always looking for the best option and our default is that every time we can use one of the cabinetmaking programs that’s what we do.
“In the case of Southern Alberta, the indigenous community we are working with has a training centre, so we were able to rent a bay there and set up a shop for our class in their facility.”
Lipman says they were really fortunate in that case as well, because they found a local instructor who was a very experienced red-seal guy in construction carpentry with a real interest in having the youth succeed and delivered that program.
“We have been there for close to four years now and he has been the instructor who has looked after the shop and participants. It has worked out really well.
“The idea for these programs is to create good quality workers for entry-level positions for the industry. These are not apprentices coming out of our pre-employment course, but they have good basic skills and an understanding of the industry,” he says.
“And in many cases, we’re able to negotiate a work experience component so that they get six to eight or even 12 weeks of experience to try out their skills and work with a business to experience the work.
It also gets them into the door so they can show off their skills and that they are interested in the job and they may be able to land a permanent job and work their way up. Then the manufacturer takes over the training as necessary.”
What can you do
for a company looking for workers?“If we were to do a program in Moncton for example, we would contact local manufacturers to see if they are interested in offering a work placement to someone with some good entry-level skills. That then creates an opportunity for those manufacturers to invite a student to come in, which is good for everyone involved.
“It gives the student a chance to experience the job and the manufacturer can see if that person might be a good fit for the company.”
Of course nobody can guarantee employment, but Lipman says they try and put the right people and companies together and they always try to prioritize these sessions in areas where companies are looking for employees.
In some cases, and depending on the funder, program participants might get paid or they might get a training allowance.
“I also want to mention that some funders want us to work with a specific demographic, for example immigrants and newcomers and we will then design a program specifically for them,” Lipman says.
Some of their programs are national or regional in scope and other times there are situations where it’s local manufacturers that have asked the government to fund some local programming.
“We’ve even had a couple of cases where we have done the training right on the floor of a manufacturing company, once in New Brunswick and once in Ontario. That was some time ago, but it looks as though we might have another one of those coming up soon. In that case the manufacturer gets a greater opportunity, but they also contribute more to the cost of the program.
Lipman says they biggest challenge is to find funding to be able to offer their programs.
“We recently completed our Ottawa project, which lasted three years. So now we are back at the proposal stage looking for funding. “Funding is always the challenge, that’s really the only limiting factor as we could run multiple programs in multiple regions simultaneously if the funding is there.
“And since most of the delivery is done by local experts, we don’t have to be there all the time, but we are the facilitators and organizers. We get heavily involved in the setup and make sure the logistics are in place and the recruitment. But once that has been set up, the program is run locally and we are fortunate Norma monitors closely to ensure successful outcomes.”
Lipman says the Wood Manufacturing Council organizes the complete package. It starts with finding a location, then secure the funding and, last but not least, secure a facility and instructor.
“We basically go in and negotiate the whole package. From funding to execution, so that’s all handled by us,” he says
“So once we tell people about the program, they don’t have to worry about anything. We try to make it so that it is just a one-stop-shop.”
“So if there is a wage subsidy or training subsidy available, we tell them about it up front, it’s all part of our recruitment. That means participants know they will get industry experience, they will get their safety tickets, their essential skills training and time in the shop and an allowance for training and the manufacturer could get a wage subsidy.”
Government fundingThe funders are usually federal or provincial governments, and the fundamentals of their programs are based on the aforementioned results from WMC’s big labour market survey.
“So it’s not us who just make something up, we are responding to industry need and this is truly by industry for industry,” he says.
So the companies and colleges helped us develop all of our products and services so they are accurate and relevant and useful to the industry.
More coursesIn addition to the pre-employment program, WMC also offers courses in everything from exports skills development programs, learning and enhancing essential skills and online management training through UBC’s CAWP.
The Wood Employee Readiness Curriculum (WERC) is a multi-week pre-employment program for target and equity groups.
While initial efforts to attract non-traditional employees were focused on equity groups to help the industry develop a more diverse workforce, the WERC program now provides career opportunities for new Canadians and workers with basic skills. WERC is also offered to a broader audience with programs available for disadvantaged youth, women in non-traditional trades and indigenous populations. Interest in these programs is growing each year.
WMC also offers school boards and woodworking teachers across Canada access to the Wood Manufacturing Council’s WoodLINKS program materials on-line. WoodLINKS is primarily a program that connects education and industry. It is a high school curriculum for woodworking that can lead to industry-recognized certification of graduates.
WoodLINKS was created with the objective of developing a certification program, which would facilitate collaboration with high schools to train more skilled entry-level workers for the wood industry.
For more information:
www.wmc-cfb.ca
and wmc@wmc-cfb.ca